The thin aluminum flashing widely used today is inexpensive, but is a poor choice in many applications. Always choose metal flashings that are compatible with the adjoining building materials to prevent galvanic corrosion. Also choose flashings that will last at least as long as the siding or roofing materials where they are to be placed.
When incompatible metals are in direct contact, and the materials remain wet, the more active metal corrodes and the passive metal is protected (see The Galvanic Scale, below).
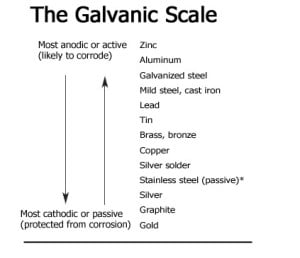
*Note: Most stainless steel used in residential construction is passive, usually Type 304. The more durable Type 316 is recommended for coastal areas exposed to salt water and salt spray.
Aluminum. Most residential wall flashing today is made from light-gauge aluminum “coil” stock because it is low-cost, easy to bend, and holds paint well. However, the aluminum alloy commonly used in flashings tends to oxidize and pit in salty or polluted air. Unpainted aluminum flashing will also corrode in contact with pressure-treated wood, concrete, mortar, or other alkaline masonry materials. Also aluminum cannot be soldered, limiting it to simple profiles.
If using aluminum, use at least .019 in. coil stock, preferably .022 to .024-in. Some home center coil stock is .017 or thinner. Choose prefinished stock for difficult environments such as urban areas with air pollution, as these are much more resistant to corrosion. However, cut edges are still vulnerable. Also be aware that the actual thickness is less than the nominal thickness on pre-painted stock. In coastal areas, .024 to .027 in. coil stock is preferable and still thin enough to be formed with a portable sheet-metal brake. However it’s best to avoid aluminum altogether if you are close to salt water. Heavier .027 and .032 in. material is called “gutter stock” and used to form seamless gutters.
Copper. Copper flashings are a good choice for many applications, but expensive. Two types are available: soft and cold-rolled. Soft copper is very malleable and useful for molding into irregular shapes. The harder cold-rolled material is a better choice for most applications, because it is stronger and more durable. Copper flashing thickness is rated by oz. per sq. ft. and is typically 16 or 24 oz.
Copper flashings are easy to solder and corrosion-resistant, even in polluted air and in contact with masonry, but should not be in contact with galvanized steel. Nails in contact with the copper should be copper or stainless steel. Over time, all unpainted copper will oxidize and develop a green patina that protects the underlying copper. This a gradual process that occurs over 5 to 10 years. While most people find the patina attractive, the runoff of the oxidation can leave streaks of blue-green stains on the siding or trim.
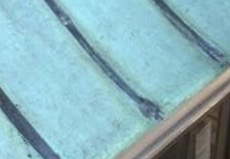
Some experts caution against using copper or lead-coated copper in contact with red cedar or redwood or rainwater that drains over the wood. Over time, the copper surface will be etched by the acidic wood runoff. Although failures of copper flashings are rare, they have been reported in areas of the Northeast after 10 to 20 years of service. The combination of acidic rain and exposure to runoff from red cedar is suspected as the cause.
Lead-Coated Copper. Copper flashing coated with lead on both sides can work well where staining of building components from runoff may be a problem. Lead-coated copper has a less noticeable gray runoff. Also, copper flashing will react in contact with galvanized steel unless the copper is lead-coated.
Lead. For special flashing applications where a high degree of malleability is required, such as chimney step flashing, lead is a good option. Lead is easy to bend and mold, and is very resistant to corrosion. Lead is relatively soft, however; so it should not be used where it will be bumped or walked on. Also, it is best to leave lead flashings unfastened on one side to allow movement. If pinned on all sides, the flashing can fatigue and tear due to thermal movement.
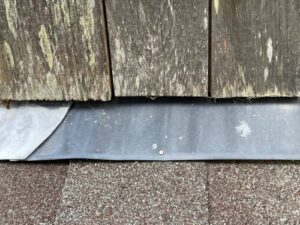
Galvanized Steel. This is the least expensive and least durable metal flashing material. It is not recommended in harsh climates or in contact with masonry materials or pressure treated wood. Like other galvanized products, the galvanic coating will eventually wear away exposing the underlying steel to corrosion. A proprietary version called Galvalume has a much longer service life, but is still not recommended for contact with masonry or treated wood. Steel flashing is typically 26 or 28 gauge, or about 1/64 in. thick.
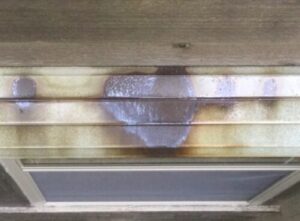
Galvanic Corrosion
With metal flashing, roofing, or any metal building components, the safest strategy is not to mix metals that come in direct contact with one another. Use aluminum flashing and fasteners in contact with aluminum, copper flashing and copper nails with copper roofing, gutters, etc. When this is not possible, choose a second metal that is not likely to lead to galvanic corrosion or use a physical barrier to separate the two metals.
The Galvanic Scale. The galvanic scale (see Table above) ranks a metal’s tendency to react in contact with another metal in the presence of an electrolyte, such as water or even moisture from the air. Metals at the top of the chart are called anodic, or active, and are prone to corrode; metals at the bottom are cathodic, or passive, and rarely corrode. The farther apart two metals are on the chart, the greater their tendency to react and cause corrosion in the more active metal. Metals close to each other on the scale are usually safe to use together.
The Area Effect. The rate of corrosion is controlled by the area of the more passive metal. For example, a galvanized steel nail (active) will corrode quickly if surrounded by a large area of copper flashing (passive). For that reason, you should never use galvanized nails or screws with copper flashing.
If a copper nail is used in galvanized steel flashing, however, the corrosion of the steel will be slow and spread over a large area, so it may not be noticeable. In each case, the active metal corrodes, and the passive metal is protected.
Where incompatible metals must be used in close proximity, use the following precautions:
• Separate the two dissimilar metals with building paper, bituminous membrane, durable tapes, or sealants so they are not in direct contact.
• Coat the cathodic (less active) metal with a nonconductive paint or bituminous coating.
• Avoid runoff from a cathodic metal (e.g., copper gutters) onto an anodic metals (such as galvanized steel).
Incompatible Materials
In addition to galvanic corrosion, a number of other common building materials can harm the finishes on metal flashing or lead to etching or corrosion of the material itself:
Wet Mortar. Aluminum flashing materials can be damaged by alkali solutions such as wet mortar. Where contact with wet mortar cannot be avoided, one option is to spray the metal with lacquer or a clear acrylic coating to protect it until the mortar is dry.
Pressure-Treated Wood. Aluminum and galvanized flashing should not come into direct contact with today’s pressure-treated (PT) wood, which contains much higher levels of copper than older CCA-treated lumber. Contact with the wood can cause corrosion in both aluminum and galvanized steel. One approach is to separate the flashing from the wood with peel-and-stick flashing tape, such as Vycor’s Deck Protector.
Another good option is membrane-type flashing, used alone or as a layer to separate the pressure-treated wood from the metal flashing or steel framing connectors. Other options, although more expensive, include stainless-steel (the best choice for coastal projects), copper, and lead. Plastic flashings made from PVC and other plastics are safe to use, but may not be as durable as metal in most applications.
Salt Spray. Saltwater spray is very hard on steel and uncoated aluminum products and may lead to corrosion within 5 to 7 years. In these areas, the best choices are copper, stainless steel, or prefinished aluminum with a durable, heavy coating.
Palo says
Can I Use Stainless-Steel Nails with Galvanized or Galvalume?
I’m having asphalt shingle roof replaced with painted galvanized drip edge and galvalume valleys. I’ve requested stainless steel nails for shingles, and roofer recommended stainless nails also for valleys and drip edge. Is this correct? House is about 5 miles from ocean in central east coast Florida. Thanks.
buildingadvisor says
I would not recommend stainless steel nails for galvalume or galvanized drip edge. Stainless steel is far away from galvanized and aluminum on the galvanic table in the article Metal Flashing Materials. This indicates a high degree of potential for corrosion to either type of sheet metal, if the metals are in contact in the presence of water. Five miles from the water may increase the rate of corrosion.
The stainless-steel fasteners (the passive metal) will be fine, but you are likely to find some localized deterioration of the other metals where the nails penetrate. The actual rate of corrosion is difficult to predict as it is effected by a number of variables. If the nail holes stay dry, you will not have a problem. If they stay wet for long periods with salty water (a strong electrolyte) then the corrosion will be fast, but should stay limited to the area around the nails. It may also be spread over a large area and hardly be noticeable due to the “area affect”
Your best choice is always to use compatible metals for fasteners and other hardware. For galvanized sheet this is hot-dipped galvanized nails. For the galvalume use hot-dipped galvanized nails or aluminum nails and fasteners.
Eunice says
Copper vs. Lead Chimney Flashing?
We need to replace our chimney flashing. The roofer quoted lead flashing, but can also do copper instead for $300 more. He said the copper would last 50 years whereas the lead would last 20. We I’ve in the northeast. We have some environmental concerns about using lead, though that side of the roof runs off into a side yard. Also, we have aluminum gutters, so I’m wondering if the copper could cause more corrosion of the gutters than the lead, or if it would be the same. Thanks for a great blog!
buildingadvisor says
I have seen lead flashing intact on 100-year-old houses, so I’m not sure why your roofing contractor is estimating a service life of only 20 years. Both copper and lead flashing installed properly will last well over 50 years and, in most cases, will outlast the roofing material.
While lead can pose a health hazard in homes with old lead water pipes, flaking lead paint, or other means of ingestion, lead flashing is not considered a significant risk to homeowners. The amount of leaching is minimal and the runoff is usually well dispersed. However, the lead may pose a risk to installers if they do not follow recommended safety precautions, like wearing gloves.
To be extra cautious, you could seal the new lead with a commercial lead coating called patination oil. This works best when applied to the newly installed lead and may be recoated every few years. In addition to sealing the lead, it provides a uniform white patina.
As for copper flashing and aluminum gutters, there is a small risk of increased corrosion to the aluminum, especially if there is standing water in the gutters below the copper. You can see on the galvanic scale, in the article, that copper is far away from aluminum, making the more active metal (aluminum) subject to corrosion if the two metals are in contact in the presence of water.
There’s also a small risk of the copper runoff staining masonry or light-colored siding below the flashing — if the runoff is not captured by a gutter system. To prevent any problems with staining or corrosion, lead-coated copper flashing is a (very expensive) option.
As a practical matter, either lead or copper flashing will work well and will probably outlast your roof — and maybe you as well. Neither should cause any significant problems for the homeowners or nearby materials.
Eunce says
Thanks so much for the response. The roofer is proposing lead counterflashing with aluminum step flashing. Are there any issues with metal compatibility and should the metals be separated?
buildingadvisor says
Lead is a few steps away from aluminum on the galvanic scale, so there is some corrosion potential to the aluminum — the more active metal. The corrosion potential is increased if there is salt air (coastal area), air pollution, wood smoke or other factors the promote corrosion. Even in the metals are separated by a barrier, run-off from the lead could still cause problems.
It is hard to predict the rate of corrosion but, to be safe, it would be best to minimize contact between the metals. A physical barrier, such as bituminous flashing tape, works well. It can be placed over the vertical legs of the step flashing where the lead counterflashing is in contact. Most flashing tapes will deteriorate in sunlight, so the tape should only go where it will be covered.
However, lead run-off can still be a problem. The best protection would be a good metal primer and paint on the aluminum. Choose products formulated for aluminum and make sure the surface is clean. For example, Rust-Oleum makes an aluminum primer for both spray and brush application. If the aluminum is pitted or degraded, use a product like Rust-Oleum Self-Etching Primer.
Before applying any primer:
– Clean and dry the surface
– Sand the metal with fine sandpaper
– Apply the primer and lightly sand
– Apply one or more top coats
– For optimal protection, apply a clear sealer
It’s a lot of work, but may be worth the effort if you want to maximize the service life of the aluminum step flashing. The best approach, where feasible, is to use the same metal for both flashings.
mark c parsons says
Best Fastener for Copper Flashing?
What type of fasteners would you recommend when installing copper flashing, with an isolator such as forty flash with galvanized weep creed applied over. The fastener will pass thorough the weep screed, through the isolator & then through the copper into the lumber?
buildingadvisor says
I’m not aware of any metal that is safe in contact with both copper and galvanized steel.
The safest fastener material to use with copper flashing is copper. Annular-ring copper nails, sometimes called “slater’s nails” are a good choice. Stainless-steel nails can also be used as SS and copper are close on the galvanic scale, although there is some theoretical possibility of minor damage to the flashing, especially in marine or other extreme environments.
Damage to the copper would be minimal, however, due to the “area effect,” described in the article above. The more active metal, the copper, is much greater than the more passive metal, the steel fasteners. t
I did a test about five years ago with stainless steel nails in copper flashing on cedar shingles and have seen no signs of corrosion. In marine or other severe environments, however, it would be safer to stick with fasteners made of copper.
The galvanized steel is the greater problem. Galvanized should not be in contact with copper or SS. Due to the area effect the corrosion of the galvanized weep screed will be reduced, but could still be significant due to the metals’ wide separation on the galvanic scale. It would be wise to separate the nail heads from the weep screed with heavy felt paper, nylon gaskets, or any durable material that is suitable to the application.
John DaCruz says
Are Stainless-Steel Screws OK For Aluminum Skylight on Copper Roof?
We are putting and Aluminum framed sky-lite with a baked enamel finish onto a lead coated copper roof.
The skylite will be above the roof. Water will run off the skylite onto the roof. The two metal will not come in direct contact with each other other. Although a stainless steel screw which attached the skylite onto the roof may be in contact with both at two separate locations. Do you see a potential galvanic corrosion issue with what I am describing. Thanks in advance for you response. J
buildingadvisor says
The main factors to consider are the metals used, the area effect (the rate of corrosion is controlled by the area of the more passive metal), and the presence of moisture. Passive metals, like stainless-steel are protected, while active metals, like aluminum, are vulnerable to corrosion.
Areas that capture moisture and stay wet for extended periods of time are much more prone to corrosion. Other environmental conditions such as air pollution or salt air in coastal areas also promote increased corrosion.
If you look at the galvanic table, you can see that stainless-steel fasteners are likely to react with aluminum. However, since the area of the stainless steel (the passive metal) is small compared to the aluminum (the active metal), the amount of corrosion will be limited. The same is true with the lead coating. However, stainless steel and copper are close on the galvanic table so they are not likely to react.
If you have the option, it would be best to use aluminum screws in contact with the aluminum and brass screws in contact with the copper. If each fastener touches both materials, however, stainless-steel fasteners might be your best option. In that case, you should isolate the SS screw heads from direct contact with the aluminum — for example, with nylon washers.
Doug says
Can I Use Galvanized-Steel Hangers With Aluminum Gutters
I was wondering if I could use galvanized-steel eavestrough hangers with aluminum eavestroughs (gutters)?
buildingadvisor says
Aluminum and galvanized steel are next-door neighbors on the galvanic scale (see diagram above), which means that they are unlikely to cause any significant corrosion under normal conditions. In fact, aluminum coatings are sometimes used instead of zinc to protect steel.
Normal conditions means low or medium humidity levels and no significant salt, corrosive chemicals, or other pollutants in the air.
Over the long run, however, there might be some increased corrosion in the steel once the zinc coating wears off – that is, in addition to the normal corrosion that occurs in galvanized steel as the sacrificial zinc coating is lost.
Bottom line is that the corrosion potential between aluminum and galvanized steel is low, but that there is always some corrosion potential when using different metals in direct contact in a wet environments – like a rain gutter (eavestrough).
Keith says
Best Flashing Metal For Stucco?
I am redoing my roof and would like to know which type of metal can be safely used as flashing? I have the typical painted aluminum gutters. My chimney has a stucco finish. Contractors have recommended flashing made from either aluminum, copper, or “metal”. I live in a busy suburb of a major city which receives about 48-inches of rain annually.
buildingadvisor says
I’m assuming that the “metal” is galvanized steel. Where the flashing is in direct contact with stucco or is washed over by water running down the stucco, you will get the longest service life from copper or stainless steel. Of course these are also the most expensive option.
Aluminum will usually outlast galvanized steel. With any metal flashing, the heavier the flashing (and galvanized coating with steel), the better. Galvanic corrosion requires moisture and it sounds like you have a lot of it in your area. So you may want to upgrade to a non-corrosive metal, such as copper, lead, or stainless steel, especially around the chimney.
If you decide to use more than one type of metal, it’s best prevent direct contact between dissimilar metals. You can isolate one metal from the other with a durable material such as asphalt felt or membrane flashing. Also, you don’t want aluminum or galvanized flashings to come in direct contact with pressure treated lumber, which is also highly corrosive.
Sterling Hearth says
Is Aluminum Flashing OK with Galvanized-Steel Roofing?
Aluminum Flashing WITH Galvanized Steel OR Galvalume Roofing?
I am wondering if aluminum flashing that is painted or unpainted is OK to use with galvanized-steel roofing or Galvalume roofing.
buildingadvisor says
If you take a look at the galvanic scale, you can see that zinc, aluminum, and galvanized steel all sit at the active (anodic) end of the scale. The greater the distance between two metals on the scale, the more likely they are to cause corrosion in the presence of moisture.
The corrosion takes place in the more active metal and is controlled by the area of the passive metal. So, for example, a galvanized nail head will corrode quickly in a sheet of copper flashing.
Since the metals you mentioned – aluminum, galvanized steel, and Galvalume – are all active, they will all oxidize and corrode to some extent, but are not likely to increase corrosion from contact with one another. Zinc functions as a sacrificial layer in galvanized steel. Galvalume uses a proprietary coating of zinc, aluminum, and silicon that resists corrosion better than ordinary galvanized steel.
All things being equal, painted aluminum will fare better than unpainted aluminum, especially if the aluminum is protected with a a heavy factory coating. Also, you need to consider the specific application. Details that are likely to retain moisture will corrode faster than details that dry quickly. If you are near salt water, metals corrode rapidly, so even a small galvanic reaction could lead to problems.
In wet conditions, it never hurts to separation dissimilar metals, even those close together on the galvanic scale, with a non-conductive material. A carefully installed layer of asphalt felt usually does the trick.
Gary Simard says
Why is Lead Chimney Flashing Corroding?
I have lead chimney flashing that is corroding less than 3 years after installation. The step flashing underneath is aluminum. The aluminum appears to be in same condition as when installed. The lead flashing looks fine on the vertical portion of the chimney but has turned white and shows pitting and significant deterioration on the sloped portions atop the asphalt shingles. We live in the northeast and burn firewood in a wood stove which vents out this chimney. Any thoughts on the source of the lead corrosion and how to prevent this from happening again?
buildingadvisor says
Lead is a very stable, non-reactive metal, so this is a bit of a mystery. Lead, or the run-off from lead, can cause corrosion in aluminum under some conditions, but aluminum should not harm lead.
Where the lead has turned white, this is a natural patina of lead carbonate caused by the reaction of lead with carbon dioxide in the air. This white film builds up over time and protects the underlying lead from further damage. Condensation on the bottom face of lead flashing can lead to deterioration since the protective carbonate layer is unlikely to form on the bottom surface. However, in your case, it sounds like the corrosion is on the top surface of the lead.
While lead flashing is very common on older chimneys, and usually lasts for decades, under some conditions concrete or mortar made with Portland cement can harm lead. The strong alkaline solution created by the wet concrete mix can attack lead even after the concrete or mortar has cured, since some moisture remains in pores of the concrete or mortar. This is generally only a problem when the lead is embedded in concrete or mortar.
As for wood smoke, it’s true that creosote is highly acidic and corrosive to most metals, but I doubt that this is causing your problem. Another possible culprit is air pollution, if you are in an urban area. Air pollution accelerates the deterioration of nearly all building materials.
While I’m not sure of what is the cause, the best solution may be to protect the lead flashing with a high-quality paint made for metal. Start by thoroughly cleaning the lead surface, then prime with a metal primer made for non-ferrous metals, followed by a topcoat made for metal or multi-surfaces. This should protect the lead surface from direct contact with anything that could be promoting corrosion.
You could also try switching to copper, although it may not be any better than the lead you are currently using. In fact, copper flashing is often coated with lead to make it less reactive with galvanized steel.
Gary Simard says
Thank you for the quick reply.
I believe your conclusion regarding the cause is correct. The areas of the chimney that were flashed with the same lead, but are not below a mortar joint, look like new. This appears to correlate to your hypothesis.
Unfortunately the deterioration of the much of the lead flashing is to the point that replacement is necessary and coating with a paint a bit too late.
I’m still of the opinion that lead is a superior material for chimney flashing rather than aluminum. It also has the significant advantage of being highly malleable so it’s great for fitting around tricky corners and slopes, of which where my chimney meets the roof has plenty.
I could treat the mortar with a sealing agent.
However, I’m still puzzled by the mystery of why a stable material like lead would deteriorate so rapidly. Lead flashing on chimneys needs to be embedded into the mortar in order to be create a watertight joint. Wondering if there is possibility I purchased a bad batch of lead or used the wrong mortar? Guess anything is possible with the process of smelting lead but have you ever heard of poor quality control or lead that was contaminated with impurities that would induce premature corrosion?
I’m more than willing to buy more lead but I don’t want to make the same mistake twice.
buildingadvisor says
I agree with you that lead (or copper) is the material of choice for chimney flashing. I am also puzzled by its failure in three years.
Most lead flashing is over 99% pure lead. It’s possible that you got a bad batch, but not likely. I would suggest buying from a contractor lumberyard or masonry supply house rather than a home center. Home centers have many perfectly good products at good prices, but some are poor quality.
When you replace the flashing, I would recommend sealing the embedded the flange with sealant rather than mortar. Use a polyurethane sealant such as Sikaflex or Loctite and make sure it’s a “non-sag” formula suitable for vertical applications. You’ll want to create a professional-type sealant joint with backer rod keeping the sealant bead about twice as wide as it is deep, as in the illustration below. Polyurethane sealant is pretty messy and difficult to tool, so best to practice first on a test joint – and wear gloves.
Sealing the mortar might also help. The only type of sealant you should use on masonry (brick, mortar, concrete) is silane or siloxane, or a mix of these. Silane/siloxane are penetrating sealants that allow the masonry to “breathe” and dry out when necessary. They will limit the intrusion of moisture into the mortar and are usually used to protect the mortar. In your case, sealing may also help protect the flashing if the cause is alkaline water leaching out of the masonry.
Many years ago a friend of mine got third-degree burns on both knees from kneeling on wet concrete for a few hours while finishing a slab. This drove home to me the corrosive power of wet Portland cement. I always wear rubber gloves and other protective gear when working with concrete or mortar.
Best of luck!
heli wolk says
Is Copper Compatible With Aluminum?
If all the valleys and gutters on a roof are made of copper, is it OK to install chimney flashings made of Fast Flash and Colorbond?
According to the supplier (in Sydney, Australia) Fast Flash is “Flexible self adhesive flashing made from Aluminium stretch netting cast in flexible polymer rubber with a self-adhesive backing.”
I am not sure what Colorbond is made from.
I am particularly worried about the interaction of copper and aluminium, and also whether the polymer rubber would have a short life due to UV exposure.
buildingadvisor says
Fast Flash is not sold here in the U.S., so I am not familiar with it. Based on the manufacturer’s (DEKS Industries) description, it is similar to the self-adhesive flashing tapes sold here, but is designed for UV exposure and reinforced with an aluminum fabric. It is sold with a 20-year warranty.
Most membrane flashings in the US, including the higher quality butyl tapes, are not intended for long-term UV exposure. However, UV additives can be added to synthetic rubber compounds to give them long-term durability in sunlight. For example, EPDM roofing can last for decades in full sunlight. I would suggest contacting the company’s technical services department for more detailed information about UV resistance.
As for the aluminum reinforcing, if it is fully embedded in the membrane, it should not pose a problem with copper. However, copper and aluminum do not play well together as they are pretty far apart on the galvanic scale, which you can in the article above. Where two incompatible metals are in contact, in the presence of water, the more active metal (aluminum) corrodes. The rate of corrosion is controlled by the relative area of the passive metal. So, for example, aluminum nails would corrode rapidly in contact with copper flashing.
If the two metals are not in physical contact, however, I wouldn’t be concerned unless there is a lot of water runoff from the copper to the aluminum. In that case, the aluminum might be subject to accelerated corrosion from copper particles in the runoff.
Colorbond is a proprietary pre-painted steel roofing material and flashing made in Australia. The paint is factory applied to a galvanized steel base with an aluminum/zinc-alloy coating. The material is very corrosion resistant and recommended for coastal and industrial environments. However, like all galvanized steel products, it is not compatible with copper and brass, or lead (more so because of the aluminum content). The manufacturers of Colorbond, recommend no direct contact with these metals or even with runoff in contact with these metals.
When in doubt, it’s best to avoid mixing metals. Anything far apart on the galvanic scale will be problematic for the more active metal, the one higher up on the chart. Hope that helps!
Brian says
Bonderized Steel vs. Copper or Stainless
I live about 1/4 mile from the ocean in California, and need to replace the corroded flashing and the surface material on my roof deck. The flashing goes under a stucco wall that surrounds the deck. I know that stainless steel or copper flashing would be good choices for this, but was told by a contractor that bonderized flashing would be fine and much less expensive. I am trying to decide whether to pay considerably more for stainless steel flashing. How long would bonderized be expected to last vs. stainless steel for this application?
buildingadvisor says
A lot of factors affect the longevity of flashing, so it’s impossible to provide exact numbers. I’ve seen deck flashing where one piece has rusted through and a piece two feet away, in the identical application, looks fine.
The biggest factor that affects longevity is exposure to moisture, especially retained moisture that does not readily dry out. Direct or indirect contact with incompatible materials is also a big factor. “Indirect contact” means that the flashing does not touch the incompatible material, but rainwater washes some of the material down onto the flashing. Both masonry, including stucco, and pressure-treated wood will accelerate the deterioration of galvanized steel and aluminum. Salt spray in the air is also hard on most metals, especially steel.
Bonderized steel is galvanized steel that is chemically cleaned, rinsed, and treated with a thin zinc phosphate coating that produces a dull gray finish ready for painting. The finish acts like a high-quality primer, extending the longevity of the paint, but not significantly increasing the service life of the underlying metal. Bonderized steel should be painted as soon as it is installed or is prone to form “white rust,” a white, powdery film of zinc oxide that can harm the finish.
All things being equal, stainless steel and copper will long outlast galvanized steel. Assuming that the flashing is 26- or 28-gauge G-90 steel, a reasonable guestimate is 20 years of service life for the steel flashing, maybe less because of your proximity to salt water.
Stainless-steel or copper, on the other hand, will probably outlast you. I would suggest looking at the extra material cost as a percentage of the entire project and decide if the peace of mind is worth the added expense. Best of luck!
Patty says
Is Copper Compatible with Aluminum?
Making a chimney top with copper over top aluminum – does there need to be a barrier between the two because of heat, ash, or wood.?
buildingadvisor says
If you take a look at the Galvanic Scale, above, you can see that copper and aluminum are spread far apart.and aluminum is the more active metal. THis means that the aluminum is likely to corrode if the materials are in direct contact in the presence of moisture. Short answer: yes, you would be wise to place a durable physical between the two metals. Good quality asphalt felt paper is one option. A more expensive and longer lasting approach would be to use a self-adhesive flashing membrane.
Barbara says
What Copper Cladding Will Turn Gray?
Looking for a coated copper to put on front of a new 3rd story addition to my center-city townhouse. I don’t want it to go to verdigris (blue-green patina) — instead I want it to turn grayish over time. What is recommended?
buildingadvisor says
Revere Copper Products (as in Paul Revere) makes copper roofing and cladding coated with a tin-zinc alloy, which it markets as Freedom Gray. The material is prepainted with a temporary gray finish and weathers to a uniform dark gray.
Another option is to use pure zinc or zinc alloys, which weather to various shades of gray. Products on the market include Rheinzink which is available in a blue-gray or graphite gray finish, and VMZinc, which makes a wide variety of zinc roofing and cladding products with various finishes including slate gray. Natural zinc tends to oxidize to a slate gray tone.
Lead-coated copper is also sometimes used. It typically weathers to a dark gray, but may turn reddish after a few years depending on environmental conditions and the product’s specific formulation. In some applications, environmental issues with lead may be a concern, as small amounts of lead leach off with the rainwater.
Many of these materials are primarily used in commercial projects, so they may be easier to locate and specify the proper installation details if you are working with an architect.
Any of these materials will perform well over many years, but may not give the exact look you are seeking, or may end up streaked or staining other materials below if they are installed to the manufacturer’s specifications. Best of luck with your project!
Barbara says
Wow – almost instant response!
I am working with an architect and she will order the materials. We’re trying to duplicate the beautiful gray copper 3rd floor mansar- style front of a house nearby. By neither the owner or the architect of that renovation kept the records about the copper product. They don’t remember if the coating was zinc or lead.
So – I am very appreciative of your detailed response. I’m hoping this will remind that architect what product he found/used so my architect can try to get it for me (I was warned that it’s pricey – good thing I don’t need much :).
Thanks sooo much!
All the best….
Joanne Ikert says
Could I put a layer of stainless steel flashing right over top of my metal flashing. I am putting a concrete patio right up to it . I spoke to you earlier and you confirmed that the flashing I already have on will pit. I have been told that stainless steel flashing will not pit.
Mike Blattner says
Will Copper and Steel Contact Cause Corrosion?
My project has a shallow pitched roof that is surrounded by parapet walls. The top of the walls have been capped with copper. The flashing used on the inside of the walls is steel that has been coated with Kynar paint.
The is a small contact area between the copper cap and Kynar coated steel flashing.
Should I be concerned ??
buildingadvisor says
When copper is in contact with steel, and the area stays wet for extended periods, the active metal – the steel – will corrode. The passive metal, the copper, is protected.
The larger the passive metal is relative to the active, the greater the corrosion. For example, steel nails will rapidly corrode when used to fasten copper flashing.
To be safe, it is best to isolate the two materials. Kynar is a high-performance coating and should do a good job of protecting the steel, but you could certainly get some corrosion at cut edges or nicks that expose the underlying steel.
To be on the safe side, you should consider separating the two materials with a physical barrier such as peel-and-stick flashing tape (as long as it is not exposed to sunlight) or any non-conductive material such as plastic or wood.
Joanne Ikert says
Will Concrete Cause Corrosion in Metal Cladding?
I have just built a new house and have painted tin cladding around the base of the house. I am going to have concrete poured and have heard that the cladding against the concrete will rust within a couple years. Sure don’t want that to happen!
What would be a good solution for this?
buildingadvisor says
Concrete, mortar, and other alkaline masonry materials can cause corrosion when in direct contact with aluminum and galvanized-steel flashing or cladding materials, which is probably what you have.
It’s unlikely that you have tin cladding. Tin-coated steel, called “tinplate” was used on some older roofs and decorative exterior components, but is rarely used in new home construction.
A heavy factory-applied coating on aluminum or galvanized steel can prolong its life, but it’s best to use a more durable metal such as copper or stainless steel in direct contact with concrete.
Another option is to create a physical a physical barrier between the metal and the concrete. Peel-and-stick flashing tapes, made from synthetic rubber membranes, are often a good option as they are long-lasting and durable as long as they are not directly exposed to sunlight. Depending on the specific detail, you may be able to find a durable plastic or vinyl molding or trim piece to protect the metal.
Also, pay attention to drainage of water where the two materials meet. Water is required for corrosion, so the longer this area stays wet, the more rapid any corrosion will be.
Joanne says
Thanks for the advice. If I could find a vinyl siding material that matched my colors, could I glue that onto the flashing material. Would that work. I have also been reading about N0xyde. Do you know if this would be a good option for this purpose.?
buildingadvisor says
These both sounds like good solutions – you’ve obviously done your homework here.
Vinyl siding is thick, durable, and UV-resistant, so it should work well as a barrier between the metal cladding and the concrete, as long as you can keep it in place. I’m not sure what the exact building detail is, but a mechanical solution is usually preferable to an adhesive. If you need to use an adhesive, it must be water-resistant and compatible with vinyl – for example, Liquid Nails Siding & Trim Construction Adhesive.
A heavy coating such as Noxyde could also work, but you are relying on a thorough application without any exposed metal. Peganox (now sold by Rust-Oleum) is Noxyde specifically formulated for brush or roller application, rather than spraying. Noxyde was developed as an industrial coating for metal in harsh environments and provides a thick and flexible rubberized skin, so it sounds like a good option. To achieve an adequate thickness, you should probably use two coats. You may need to buy it from an industrial supplier.
Best of luck with your project!
Charlie says
Copper vs. Painted Aluminum Flashing
I’ve got a bay window that is leaking at the seals…evidently the existing flashing was not done properly and needs to be replaced. I have two estimates for copper and for “black metal”. The copper is twice the price. Is it worth it? I don’t know what metal was/is in the existing flashing area. Thank you!
buildingadvisor says
The black metal is most likely aluminum coil stock that is pre-painted or powder-coated. It could possibly be galvanized steel. Check with the contractor. White aluminum gutters, which typically last for decades, are a good example of heavy-gauge, pre-painted aluminum.
In either case, the thin color coating is more for appearance than corrosion resistance, so the longevity and durability is about the same as with standard mill-finish aluminum or steel. As with any metal flashing, the thicker the flashing the better.
If the original flashing corroded, then you might want to spring for copper, which will outlast you. If it leaked for other reasons, then aluminum might be fine. Aluminum is the most common residential flashing material because it is inexpensive and pretty durable. If you have aluminum flashing on the rest of your house, then it will probably work here as well.
However, aluminum not a good choice in corrosive environments. Salt air in coastal areas and air pollution can be corrosive to aluminum and steel. Also algae-resistant shingles, which use copper granules, can be corrosive to aluminum and steel flashing.
You can read more on power-coated metal at these links:
Deck Fasteners Powder-Coated Flashing
Best of luck with your project!
Charlie says
Thank you so much! Excellent advice!
Al says
Will Copper Flashing Corrode Aluminum?
I’ve got a reroofing project where we have a stone chimney that has copper cap flashing that someone has installed a membrane lap and apron flashing below. When we repair the roof, I want to replace the membrane flashing with copper. I’m wondering if we can use a prefinished aluminum drip edge without it suffering damage from the copper chimney flashing, which is about 6′ away up the roof. This is a budget consideration to not use a copper drip edge if we don’t need to.
buildingadvisor says
Contact between copper and aluminum, in the presence of water, will definitely lead to the premature pitting and corrosion of the aluminum. How fast this occurs depends on a number of variables – particularly the aluminum alloy used, frequency of wetting, and the surface area of the copper (the passive material) relative to the aluminum (active material). A large area of copper can rapidly corrode a small area of aluminum, such as a fastener, due to the “area effect”.
The fact that the materials are separated by six feet is in your favor, but of course water runs downhill and will continually leach a little bit of the copper onto the aluminum. For example, algae-resistant shingles made copper granules can destroy aluminum gutters in several years in a rainy climate. In this case the copper granules are designed to carry dissolved copper down the roof surface.
In your case, the corrosive effect will be much less, but you may notice some pitting in a few years. If you go with aluminum drip edge, look for a heavy-gauge, pre-painted stock. How much protection you’ll get with the typical light-gauge, pre-painted drip edge from your local home center is hard to say. To be on the safe side, you might consider using copper drip edge just in area below the chimney flashing.
Barbara Hall says
Best Flashing for Coastal Home?
Two years ago, I had powder-coated aluminum flashing installed on two large exterior balconies. The flashing is in contact with vulcrum (not sure of spelling) and is cover on the superior surface with porcelain tile. Now the flashing has completely disintegrated pushing up surface tiles and requiring tile removal and replacement. I live at the beach 3 houses back from the actual ocean. What product should be used on the reinstall and what happened?
buildingadvisor says
I think you might be referring to Vulkem, which is a polyurethane sealant and is not corrosive to metal. However, salt air and salt spray are highly corrosive. It’s also possible that the flashing was in contact with pressure-treated wood, which can be very corrosive as well.
If you are three houses in from the ocean, you need to use a non-corrosive metal. Your choices are copper, lead-coated copper, and stainless steel. All three are expensive, but should last 50 years or more.
Copper would be fine as long as you don’t have redwood or cedar nearby which can stain or be stained by the copper flashing. Also, the copper with develop a greenish patina over time. If you use copper, only use copper or stainless steel nails to avoid galvanic corrosion.
There are some less expensive laminated copper flashings such a Cop-R-Shield, made for pressure-treated decks, but I don’t think they would be a good choice here.
Lead-coated copper is a variation that eliminates the staining issue as well as the patina.
Stainless steel is the most expensive and least reactive metal you can use. It is the fix-it-and-forget it choice and the best choice for most exposed metal hardware, flashings, nails, and fasteners in a coastal home. While the material is expensive, as a percentage of the total cost of a home, it’s not that significant.
Type 304 Stainless steel is fine for most uses. The more expensive Type 316 might be used for critical details with direct exposure to salt spray.
Another product widely used in coastal climates is PVC flashing. It is corrosion-proof, but does not have the strength or long-term durability you are looking for.
Best of luck with your project!
David says
Looking For Box-Shaped Gutter
I am looking for a box shaped rain gutter, with straight sides, similar to this image.
It could be a rain gutter or some type of roof flashing. I am not using it as a rain gutter but for an alternative use- I use them for growing microgreens.
Any suggestions on a piece of metal this shape, that I can find at a normal hardware store or order easily online?
buildingadvisor says
Here in the U.S., this is not a standard gutter or flashing profile, so I doubt you would find it premade. You would need to find someone with a sheet-metal brake to form it out of “gutter coil” which is thick aluminum coil stock — .027 in. and up — often used to fabricate seamless gutters on the jobsite.
Anyone who installs vinyl siding has a portable sheet-metal brake and this is an easy shape to form, so it shouldn’t cost an arm and a leg.
You could also contact a sheet-metal shop, metal roofing company, or heating/ac contractor who works with metal ductwork. All of these folks could easily fabricate what you are looking for. Not sure what type of metal you want for growing, but aluminum and galvanized steel would be your cheapest options. Best of luck!
Bob says
PVC-Coated Aluminum For Treated Lumber?
Will PVC-coated aluminum coil stock work well as a flashing for a pressure-treated deck?
buildingadvisor says
In general, aluminum flashing is not recommended for direct contact with pressure-treated lumber. Starting in 2004, the preservatives used in pressure-treated lumber and decking were modified to eliminate the arsenic. However, the copper content was increased and the lumber became much more corrosive to aluminum, steel, and other ferrous metals.
While, in theory, pre-coated aluminum might be OK, exposed edges at cuts and nail holes are vulnerable. Also the quality and thickness of the coatings vary and accurate specs are often difficult to obtain. Also, the PVC coating used on coil stock is really just a vinyl-based paint and is probably no more durable than other pre-finished aluminum stock.
A number of variables determine the rate of corrosion here: the specific type of pressure-treated wood, the thickness of the coating and the underlying metal, the amount of moisture that reaches the flashing, and other corrosive effects from air pollution and salt air (in coastal areas).
For critical flashings, such as over the deck ledger, where leakage could lead to structural decay and deck collapse, I would steer clear of aluminum. Better choices are bituminous membranes, copper, or high-quality PVC. In some cases it is possible to isolate the aluminum from contact with the pressure-treated wood by using a piece of membrane flashing or heavy felt paper. But I don’t recommend taking chances with the deck ledger or other structural connections.
In fact, all fasteners and connectors in contact with pressure-treated wood, including lag screws, bolts, decking screws and joist hangers, should be made of corrosion-resistant materials. Stainless-steel is the first choice for screws, bolts, and connectors and is recommended coastal environments and other harsh conditions. Heavy galvanized connectors, rated G-185, are the next best choice for steel connectors. For screws, lags, and bolts, G-185 steel and proprietary coatings, specifically tested and approved ACQ and CA lumber, are also good choices.