Flashing membranes are now widely used to prevent water leakage around windows and doors and other trouble spots on walls. Sold as flashing tape, flexible flashing, and peel-and-stick window flashing, these narrow rolls of rubberized asphalt membrane can solve many flashing problems if installed correctly. Non-adhesive versions of the same material are also available.
This is the same peel-and-stick membrane used for over 40 years to prevent roof leaks at the eaves and other roofing trouble spots. The original membrane flashings, introduced by Grace (now GTP) in 1978, were called “eaves membranes” and were 36 in. wide, designed to prevent leakage from ice dams along the lower edge of the roof. In the 1990s, manufacturers started offering similar materials in narrower rolls, typically 4 to 12 inches, for use on wall (see Photo).
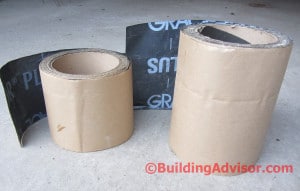
Adhesive flashing tape comes in a variety of widths for different applications. Moldable versions can be easily formed into window pans. Photo by Author.
The narrow rolls of membrane were introduced as a solution to water leakage around window and door openings and other trouble spots. Window flashing methods that worked reliably in older homes did not work well with the advent of plastic sheathing wraps, flange-style windows, rigid foam insulation, and a host of modern building techniques. The problems were hidden from sight for a few years, but came to light dramatically with a number of high-profile lawsuits by condo associations and owners of commercial buildings.
Sadly, owners of single-family homes often had to take it on the chin and pay out of pocket to replace or repair windows, trim, and the surrounding structure long before their normal service life. Trying to file a warranty claim with a contractor or window manufacturer typically lead to a classic finger-pointing exercise where each party blames the other and you’re left holding the bag.
While the peel-and-stick bituminous membranes are not a cure-all, they have proved a useful tool in the ongoing battle against water intrusion in modern homes. They simplify the task of creating a continuous barrier to water entry around doors, windows, decks, and other problem areas like the intersection of walls with roofs, decks, other building components. Unlike metal flashings, the membranes can be easily shaped or folded to protect areas that in the old days might have used custom lead or copper flashing with solder joints – not an economical option for most projects today.
Another potentially big advantage is that they can form a waterproof bond to a wide variety of materials including metal, vinyl window flanges, wood, OSB, and even plastic sheathing wraps (see Photo).
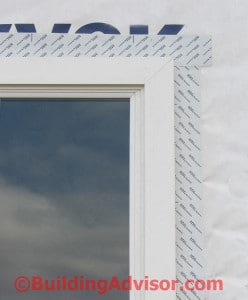
Self-adhesive flashing tapes are widely used to seal around modern flange-type windows. Photo by author.
In theory, this solves a multitude of flashing problems around windows. In addition, the materials self-seal around nail holes, a property that has made them especially useful on roofs.
But do they stick to everything? In practice, most experienced contractors do not rely on this bond to last forever – especially to OSB, wood, and plastic sheathing wraps, materials that are notoriously difficult to bond to. Some peel-and-stick manufacturers provide specific requirements for priming of OSB, masonry, and other materials before bonding the flashing. And there may be cautions in the fine print about application conditions such as temperature, moisture levels, dirt on surfaces, and the pressure the installer needs to apply for a good bond. Cold temperatures and wet or damp surfaces are a problem for most tapes. When in doubt, wait until it is dryer and warmer and use a primer on OSB or plywood.
Running a hand pressure roller over the tape will provide a better bond than simple hand pressure. The best approach, in all cases, is to not rely on the bond lasting forever, but to apply all flashing materials lapped to shed water – following the shingle principle.
Types of Flashing Tapes
Most membrane flashings come in rolls from 4 to 12 inches wide. The body is a rubberized asphalt material, faced on the outer surface with reinforced polyethylene or foil. The adhesive side is protected by a peel-away release paper. Some products, such as Vycor, have a cord to pull that lets you peel one half of the release paper at a time – very handy with wider rolls because the stuff is extremely sticky and may be hard or impossible to reposition.
The foil-faced products can be left exposed to the weather, whereas the plastic-faced flashing membranes should not be exposed to sunlight and weather for more than 30 days (longer for some brands) since UV radiation will degrade the material.
Modified Bitumen vs. Butyl. Most flashing tapes are made from SBS-modified bitumen, the same rubberized asphalt used in eaves flashing on roofs. These have a distinctive asphalt odor.
Most manufacturers also offer a more expensive butyl-rubber flashing with a butyl-based adhesive. Butyl flashings are easier to apply in cold weather and are more stable at high temperatures, making them less likely to ooze out and stain materials. Butyl flashings also bond better to difficult substrates than bituminous membranes. Also, because the butyl adhesive sets more slowly, the installer can peel off and adjust the tape during installation, a nice feature when you need it.
The higher performance of butyl comes with a higher price tag — typically about twice the price of bituminous flashing tapes.
Moldable Flashing. Dupont introduced the first moldable flashing tape, called Tyvek FlexWrap, with a wrinkled facing that allows the material to be easily molded to irregular shapes. Also called “flexible flashing,” this proved to be a popular solution for curved head flashings above round-top windows and the “pan flashing” that lines the framing at the bottom of windows and doors (see Photo).
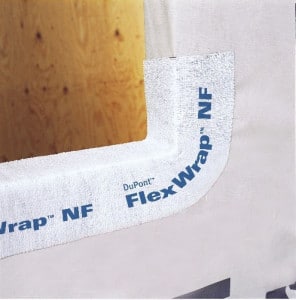
Other manufacturers, such as James Hardie (HardieWrap Flex Flashing) have followed suit with similar moldable products. Despite higher material costs, labor savings and simpler installation make these flashing tapes appealing for tricky applications.
Installation of Flashing Membranes
To obtain good results with flashing membranes and maintain warranty coverage, it is critical to follow the manufacturer’s installation instructions. These vary from product to product, but generally they address the same issues: installation techniques, application temperatures, priming of certain materials such as masonry and OSB, and compatibility with substrates (what your sticking to) as well as surrounding materials that come into contact with the membrane.
Cold and Hot Temperatures. In general, the rubberized asphalt (modified-bitumen) products do not work well in cold weather. Most become less sticky at around 50°F and will not stick well below about 40°F. Unless you are working with a rubberized-asphalt membrane formulated for low-temperature usage, a butyl-based membrane is a better choice in cold weather.
High temperatures can also be a problem for rubberized-asphalt membranes. At high temperatures and pressures, for example, when squeezed under a dark-colored metal flashing exposed to direct sun, standard modified bitumen will soften and begin to flow. The flashing will deteriorate and leave dark stains where it oozes out of the joint in the roofing or siding. In hot climates, roof temperatures often reach 150°F or higher.
In general, butyl membranes are more stable at higher temperatures, but also have upper limits. Unless specially formulated for high temperatures and labeled “hi-temp,” flashing tapes begin to soften at somewhere between 120°F and 180°F. Some high-temperature formulations made for commercial applications can tolerate temperatures over 200°F, but are generally not as sticky and may be difficult to locate. If the manufacturer does not publish the upper-limit “service temperature” contact them for this information.
Substrates. Each manufacturer specifies which products are safe to stick to and which require priming. Solid wood, plywood, vinyl window flanges, and metal are usually fine as long as they are free of oil and dirt or dust. Most manufacturers recommend that concrete and masonry be primed, and some require the priming of OSB and gypsum sheathing (used mostly in commercial building) as well. Some manufacturers recommend that all substrates be primed for best performance of flashing membranes, especially in cold weather
Windows and door details. Flashing around windows and exterior doors is number one use of flashing tapes. There are different opinions on which is the best detail, but all follow the general approach shown here.
Some manufacturers of flashing tapes claim that their products will bond satisfactorily to both plastic sheathing wrap and asphalt felt (tar paper) as long as they are clean, but few guarantee this in their product literature.Do not expect a good bond to dirty plastic housewrap that has been exposed to the weather for a month or to any dirty job-site material. Even under ideal conditions, however, (rarely the case on building sites) many builders know that the bond can fail over time. The best approach is to lap materials, following the shingle principle.
Follow the shingle principle. Given all the factors that can affect the longevity of an adhesive bond, it’s best not to rely on on a taped joint to keep water out of your home’s exterior. Every flashing detail, adhesive or not, should follow the age-old “shingle principle.” In this approach the upper material is always lapped over the lower material so water will naturally flow down and away from the building structure, even if the adhesive bond fails. This is how materials like roof shingles, cedar shingles, and horizontal sidings work – they shed water naturally. Peel-and-stick flashings still simplify many flashing joints, but they are not magic.
Compatibility. Modified-asphalt flashing membranes should never be in direct contact with flexible vinyl flashings or vinyl siding. The asphalt compound will draw the plasticizers out of the vinyl, causing the asphalt to soften and flow and the vinyl to become brittle. The rigid polyvinyl chloride (PVC) used in window flanges, however, is generally not a problem.
It’s also best to not apply caulks and sealants in direct contact with the modified-asphalt membranes, unless they are specifically formulated for that use. Like soft vinyl, the chemicals in sealants, including silicones and polyurethanes, may react with the asphalt, causing it to flow and stain the adjacent materials, such as window flanges.
Butyl-based flashings (as opposed to the more common modified-asphalt flashings) are compatible with hard and soft vinyl and most caulks and sealants, but they should never be installed in contact with any asphalt-based products such as roofing cement or bituminous flashing membranes. These may degrade the butyl and undermine its ability to seal. In these applications, modified-asphalt membranes are a better choice.
If you plan to stick the flashing tape to asphalt-saturated felt (tar paper), modified asphalt membranes are the natural choice, although some manufacturers of butyl tape approve of this detail. The question is whether there is enough asphalt in the felt paper to cause problems with the butyl adhesive. It’s best to check with the butyl tape manufacturer before proceeding.
Applying Pressure. You can’t just slap on the flashing membrane and expect it to stick forever. All adhesive membranes must be pressed firmly into place to ensure full contact and a good bond. Most manufacturers recommend using a hard rubber roller for best results. .
Caution: Cold-Side Vapor Barrier
Three-foot-wide sections of flashing membrane have been installed on roofs for decades with few problems. In snow country, some builders routinely cover the entire roof with a flashing membrane membrane, especially on low slopes. Some builders use a similar wide band of membrane along the bottom of walls to protect against splashback of rain and snow buildup.
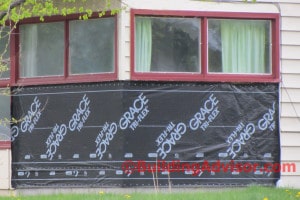
Don’t do this! Covering large areas of wall with a waterproof membrane can trap moisture, leading to rotted framing if water leaks into the wall. Photo by author
On walls, however, overuse of membranes can lead to serious moisture problems (see Photo). In cold climates waterproofing membranes on the wall exterior create a cold-side vapor barrier. Any water that gets into the wall by leakage or condensation will be very slow to dry out, potentially leading to wood decay in the wall structure.
In most cases, a section of membrane up to 3 feet wide is not likely to cause problems. However, if the wall has an imperious vapor barrier, such as polyethylene or foil, on the interior, I would avoid any large areas of membrane on the exterior.
CJ says
Seeking Self-Adhesive Membrane for Sill Seal
Greetings, I am installing a brand new metal building on a brand new cement slab. The base plates for the metal building or 2 1/2 inches wide and will be affixed to the concrete. My building is coming in September and will be assembled by a crew that delivers it. The outside dimensions are 18 x 20, So the footprint is approximately 76 feet. I am interested in a product that is self adhesive, that I can position on the concrete prior to the installation of the building. 2 1/2 inches wide by 76 feet long and prefer something that is on a roll to help prevent moisture and insects coming under the base plates. Can you recommend such a product?
buildingadvisor says
The only self-sealing sill sealer I know of is made by ProtectoWrap. I haven’t used it personally as I generally use more traditional foam sill sealers (on wood-frame buildings). But ProtectoWrap has been around a long time and has a good reputation for manufacturing air and vapor barriers and other building energy products.
CJ says
Thanks. I’ve tried to buy this product, 3 1/2“ x 25‘ rolls, the factory won’t sell it to me, the two local retailers in my area that can get it will only order it by the case and want me to take the entire case. I just need three rolls so I’ll keep trying to get it, and I’ve contacted the factory again to see if they’ll sell direct to me since I only need the small amount. Thank you though.
buildingadvisor says
Yes, special order products can be a bear — especially now when it’s pretty hard to buy any building products. There are a large number of self-adhesive flashing tapes on the market, used mainly for sealing roofs, windows and doors, and other building connections. But I would be concerned about whether they can support the load of a building without compressing or squeezing out.
Perhaps a metal flashing for insects, combined with a good quality neoprene or EPDM sill seal would do the trick. I’m not sure that the adhesive adds much value to a sill seal. Once it’s in place, it isn’t going anywhere.
C. Santos says
Source for Foil-Faced Flashing Membrane?
Where can you buy the foil-faced type of bituminous flashing membrane?
buildingadvisor says
Grace (now GCP Technologies), the original developer of flashing membranes, marketed as Ice & Water Shield, does make a foil-face version of flashing tape called Vycor Aluminum Flashing. You can find product info at this link.
Foil-faced flashing tape has the same benefits as standard flashing tape, such as self-sealing around nails, but has the added advantage of weather resistance. It is designed for permanent exposure to sunlight and weather as the foil protects the synthetic rubber membrane from the effects of UV. Standard membrane flashings should not be left exposed for more than 30 days.
To find this product locally, I would check with a lumberyard that deals mainly with contractors. If they don’t stock it, they should be able to special-order it for you. There may be other brands, besides Grace, as well.
Nowadays, you can purchase most building materials online, as well. You can purchase the Grace product online, as well, at Amazon and probably elsewhere, but I’d compare prices. Here’s the Amazon link.
Best of luck with your project!
.
Bill Schnettler says
Sticking Flashing Tape to Tar Paper
What flashing tape is compatible with grade D paper in a moderately hot climate (Jamul, CA)?
The New construction building has OSB sheathing, Marvin Integrity windows with a flange and will have portland based stucco over two layers grade D paper.. The article states some brands say that they will stick to tar paper but does not say which brand. I am hoping to find the brand. We have folded two layers of grade D paper into the opening and caulked to flange using DAP DynoFlex230, (ASTM C920). We have installed a DOW “Weathermate” sill pan.
buildingadvisor says
In general, butyl flashing tapes are not recommended in contact with asphalt products such as roofing tar, which can react with the adhesive and undermine the bond. However, some butyl tapes appear to work well with tar paper, probably because there is not enough free asphalt to cause problems.
The brand of flashing tape that I am most familiar with is Vycor, from Grace Building Products, now part of GCP Applied Technologies. Either their standard flashing tape, called Vycor Plus, or their more expensive butyl tape called Vycor Pro should bond well to asphalt-saturated building felt (tar paper), according to a tech rep I spoke with at Grace. Compatibility with felt paper is also documented in Grace Tech Letter 1.
Once the adhesive has set, he said, either flashing tape will rip the building felt before coming loose.
One advantage of butyl tape is that the adhesive cures slowly so you can peel and adjustment the flashing during installation.
Vycor Pro and other butyl flashing tapes can cost twice as much as modified asphalt tapes. They are recommended for cold-weather installations and are more stable at high temperatures, where standard flashing tapes can soften and ooze black asphalt. Butyl adhesives also provide a very aggressive bond with a wide variety of substrates.
Butyl-based flashing tapes can also be used in contact with soft vinyl such as vinyl siding and is compatible with most sealants except for some with high solvent content. High-solvent sealants can be a problem with either type of flashing tape (see Grace Tech Letter 7).
Brion Henes says
How to Flash Siding Butt Joints?
Steve, My builder used some form of flashing tape over Tyvek for the butt joints on our new LP siding. Is this an appropriate use? Thank you.
buildingadvisor says
LP, Hardie, and other manufacturers of composite and fiber-cement siding all require or recommend special treatment at butt joints to prevent water damage at cut ends. LP recommends three options to installers:
1. Gap the joint 3/16 in. and caulk.
2. Gap the joint 3/16 in. and flash (factory edges only, no caulking)
3. Hide and protect the gaps with H molding.
The gap is required to allow for linear expansion as the siding absorbs moisture and acclimates to local moisture conditions. In my opinion, the caulking approach is the most difficult to get right. H molding is the safest, but many people do not like the appearance. So the flashed method seems to be the most popular.
Most contractors use small pieces of aluminum coil stock or vinyl flashing, such as BearSkin Joint Flashing. With wood siding, many use 30# felt paper for the flashing. The flashing covers the butt joint in the siding and should extend nearly to the bottom of the siding, lapping over the top the siding piece below. It should extend upward to at least an inch above the top the siding joint (see illustration):
It’s best if the flashing matches the color of the siding, or is a dark, neutral color that will not be conspicuous. While most of the siding gaps should close up as the siding acclimates to local conditions, some may be open a crack seasonally (or always), exposing the flashing beneath.
Some builders use flashing tape for this application with wood siding, which does not change measurably in length, so there is little risk of exposing the flashing tape to UV which it is not designed to tolerate for more than a few months. The main concerns with flashing tapes are compatibility with the materials it contacts, exposure to UV, and exposure to high temperature, which can cause it to ooze a black residue, unless high-temperature versions are used.
If your building prefers to use a flashing membrane here, one of the thinner products, such as Vycor, would be best as it will not cause any bulging at the joints. Sticking the flashing to the Tyvek is not a problem. Getting a bond bond to wood can be a problem in some cases. However, the bond is not critical here as long as the flashing piece stays in place.
Bill Walker says
There are excellent roofing products that can be applied as a liquid right over the concrete. I would suggest one of them.
Steve Caven says
Sealing Valleys on Concrete Roof
I have a house in the Dominican Republic, built with a concrete roof. Yes a concrete roof. Clay tiles are the roofing material over an asphalt paper. The roof has a number of valleys and the valleys have leaks. Numerous superficial repairs have been attempted, none successful. What would you suggest as a better method of sealing the valleys?
buildingadvisor says
Here in the US, most roofing contractors seal valleys and other difficult roof transitions with a 3-ft-wide strip of peel-and-stick membrane flashing. The leading brand is Grace Ice and Water Shield, but other companies such as Henry Blueskin sell essentially the same product. Both companies make a high-temperature version (HT) that might be useful in your climate if you are covering the membrane with metal flashing.
Peel-and-stick membrane flashing has a very aggressive adhesive on the back protected by a release paper that you peel off carefully to install the material. Grace (now called GCP Applied Technology) recommends priming concrete and masonry materials for a good bond and sells a special primer for that purpose: Perm-A-Barrier® WB Primer.
Membrane flashings are made of a rubberized asphalt compound that seals around nails, making them the best choice for protecting valleys, skylights, and other roof transitions. However, these membranes cannot be exposed to sunlight for long periods of time, so they need to be covered with a protective layer – usually metal flashing in a roof valley.
Best of luck with your roofing project!
Christopher says
Steve, did you ever find a solution to your problem? We have the exact same situation with a place in Mexico… concrete roof covered by cantera stone. We’ve tried sealing the cantera with every conceivable sealer but the problem persists. Before the stone was installed a layer of “impermeabilizante’ was painted over the concrete but clearly that wasn’t enough to prevent the problem. Short of ripping up all of the cantera we’re at a loss of what to try next. Curious to know if you found any solution.
Hamid says
If you would like to do it more traditional, I would recommend a minimum of two layers of tar and one later of fabric between over the concrete structure sloped to the drain, For a better performance, you can double the waterproofing membrane (i.e., tar + fabric + tar + fabric + tar).
The assumption is that the concrete structure is already sloped into the drain; if not, you need to create the slope first by adding a layer of lightweight concrete over the concrete structure.
Bill Walker says
There are excellent roofing products that can be applied as a liquid right over the concrete. I would suggest one of them..