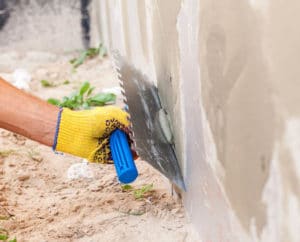
Q: The foundation on my 1980s-era house is insulated on the exterior with sheets of foam board. Several inches of foundation are exposed above grade, where the foam is protected by aluminum flashing. The foam and flashing are unsightly.
Would it risk termites or other problems to raise up the ground level with soil or river rock to cover up the foam? Are there better foundation insulation coatings to cover and protect the foam? Thanks. – Robert T.
A: While widely used at one time, exterior foam insulation on basement walls is less common today. I’m not a big fan of exterior foam insulation on foundations for some of the reasons you mention. It is difficult to protect during construction and after the home is completed. Most foundation insulation coatings deteriorate over time. And it also provides easy access to the house for subterranean termites as well as ideal nesting material for carpenter ants.
On the plus side, it allows for continuous insulation for homes with exterior foam on the walls. It also provides a small thermal mass benefit, although this is mainly true in climates with wide daily temperature swings above and below the comfort zone. An example would be the high deserts of the Southwest. And even in these climates, the benefit would be primarily for above-grade walls, not foundation walls.
Clearance to Grade
Since you already have foam insulation in place, however, you will need to find a suitable retrofit product to protect it or remove the above-grade foam (and add interior foundation insulation).
Most of the materials used to protect the foam eventually get damaged by lawn mowers, baseballs, or just normal wear and tear at the ground level.
Raising the grade level to bury the foam is not a good approach. The minimum distance from grade to untreated wood is 6 in. in the International Residential Code (IRC). Some state codes require 8 in. of clearance. You can view the detail for ground clearance at this link.
I recommend a minimum of 8 in. from grade to any non-treated wood (framing, sheathing, or siding). This is a safer target since people often add mulch, pavers, or plantings that raises the grade.
The goal is to keep water away from the wood. The water can come from soil, wet leaf litter, plantings, splashback, and snow melt. In termite-prone areas, the gap creates an inspection area for termite mud tubes leading from the soil to wood framing.
So, yes, you can raise the soil level on the exterior, but should still leave at least 6 inches of exposed foundation. If the aluminum flashing is unsightly, you can consider replacing it with a more durable material.
Insulation Protection
There is no perfect material for covering and protecting exterior foam on foundations.
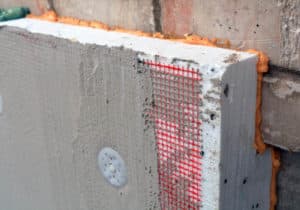
The most common approach is to apply a stucco-like “parged” finish with a surface-bonding cement. These finishes range from a thin paint-on coating to a thick acrylic-modified mortar applied over hardware cloth or metal or fiberglass lath.
The thin paint-on coatings are easily chipped and prone to peeling. Mortar with acrylic additives has the strength and flexibility needed for this application and the metal or plastic lath provides additional strength and a bonding surface with “teeth”. One benefit of mortar is that it is relatively easy to patch if it is damaged.
Others prefer panel products such as pressure-treated plywood or cement board (such as James Hardie HardieBacker). However, most cement-board manufacturers do not recommend direct contact with soil, so check first before taking this approach. Panel products can be finished with a stucco coating or exterior paint, depending on the appearance you want. Another durable, but high-cost, option is cultured stone veneer.
There are also a number of manufactured systems using panels made from fiberglass, pvc, or other materials. The main problem with these systems is that they come and go from the market. So you may end up with an orphaned system in 5 to 10 years when you need to replace a damaged panel.
Termites and Ants
Whatever system you use to cover and protect the insulation, you still have a direct conduit for termites to move from the soil to the wood structure. The termites can easily move behind the foam and escape detection.
In some termite-prone areas, codes do not allow exterior foam on the above-grade portion of the foundation, or require an uninsulated inspection gap. The gap allows inspectors to find the telltale mud tubes that subterranean termites build to travel from the soil to the wood portions of your house – their food source.
Carpenter ants also like to excavate exterior insulation to create a warm living space. While they do not eat the foam for nourishment, they can still do considerable damage to the foam.
So if you are in a termite- or ant-prone area, you may want to consider moving the insulation to the interior side of the foundation wall. In any event, you should check first with a termite expert for an effective treatment strategy.
Interior vs. Exterior Insulation
With interior foundation insulation, you can add whatever thickness you want and use any type of foam. By insulating the band joists, you can get continuity of insulation from foundation to above-grade wall.
You avoid all the issues with termites, carpenter ants, and finding an insulation covering that’s attractive and durable. Seems like a no-brainer to me. – Steve Bliss, Editor, BuildingAdvisor.com
Read more on Foundation Insulation
Bob the builder says
My grandfather, father, and myself have been poring concrete foundations for several decades. Your assertion that termites and other insects can somehow use some kind of gap between the exterior foundation wall and insulation applied to the exterior wall is without merit. First, the exterior concrete and footers are cleaned of debris and any concrete that may be be protruding from the pour, such as form lines resulting from concrete oozing out between forms, or protruding dimples (versus dimples) from modern form holding systems, need to first be knocked down using a cement chisel, and if necessary, ground down, and any dimples or holes patched level with mortar. It need not be perfectly flush.
Later, pressure wash the exterior to remove cement dust, etc., and then apply your waterproofing product of choice, with emphasis on places such as the footer and wall seams. There are products that can then be applied to the sealant as an insulation adhesive, but experience has taught me to only apply them to the insulation very sparing along just 2-4 inches of the insulation side being placed against the foundation wall, just to tack hold the insulation in place. Then you can seal any gaps between the sheets, fottrr, etc, with canned foam, trim, and then tape over it. I personally dont recommend insulation above grade for many reasons (uv exposure, lawnmower and trimmer line damage, etc) , and only apply the insulation below grade.
Depending on the R value of your insulation and it’s thickness, what you are now going to have to deal with, before back filling, is the exposed top of the insulation. Using canned foam, spray the top edge and once Hardened trim it to a 45 degree angle from the outside foam edge to the foundation wall and then duct tape a straight line above it. Now, using a waterproof mastic product, apply it to the exposed foundation wall below the tape, the canned foam, and 3-4 or more inches down along the insulation. Put more coats on, as desired. Once dry, backfill. And here is where experience plays in, as whatever sand or soil you backfill with will forcefully press the insulation against the foundation wall..!! No gap whatsoever… As for the merits of the waterproofing aspects of Styrofoam product, remember that it’s used in coffee cups, etc.
There are certainly many variations to waterproof a basement, and if money is no object, I’ve seen elastomeric ice and water sheets used as a substitute for either sprayed on or roller applied products, followed by insulation. And lastly, if your going to do anything, please don’t use the cheap, thin, rolled sill foam sold at the big box stores, and pay extra for a rubber product with those built in compressible ir tubes buit into it. And if need be, grind out the rough spots of the top your foundation walls prior to applying the sill rubber (a capillary water break) and any sill plate wood. And for what its worth, the majority of DIY and homeowners will do a MUCH better job sealing and insulating their foundations than the so-called “pros” I’ve seen over the yearsummer! Best regards.
Rick Scott says
Best Material to Cover Foundation Insulation
I have styrofoam concrete foundation would like have it covered to look better. What do you recommend?
buildingadvisor says
Not sure exactly what you mean by a “Styrofoam concrete” foundation. Are you using ICFs (insulated concrete foams) or some other system that uses lightweight insulated concrete?
Assuming that you have foam board or a foam/concrete mix exposed on the exterior, there are several options for improving the appearance and durability of the exterior finish.
The most common approach is to trowel or brush on a cementitious coating called parging. Depending on the materials used and application, you can create either a smooth or textured stucco-like finish.
Some cementitious finishes can be applied directly to the foam. But for a much more durable finish, it’s best to apply a latex-modified parging over a reinforcing material. The traditional approach is to use galvanized metal lath or stucco wire (looks like chicken wire, but heavier gauge). Another economical and easy-to-use option is fiberglass lath.
Other options to cover the foundation include pressure-treated plywood, fiber-cement boards approved for ground contact, or pre-manufactured panels made for this application — typically made of fiberglass or FRP.
In choosing an approach, consider the appearance, how much abuse the covering will get (from lawnmowers and baseballs, e.g.), and ease of repair.
peter says
Since I had the same question … Styrofoam – concrete foundation, for me, is a system of two walls of rigid insulation with a wall of concrete inside ie: Polycrete
I have received expert advice that the Styrofoam is to be sanded #36 grit, covered with a layer of TexNov-200 mixed with Portland cement GU, then the lath, then another mix of TexNov-200, All done at the same time in patches of 20-50 sq.ft. depending how fast you work. A finishing coat of your color choice of Sandcrete at a minimum of 3 days later.
These are Canadian/Quebec products.
Ladislav says
I have used on my house to protect the 8″ of Styrofoam from the sun by the 1/2″ Wonderboard.
Mind you – the soil is 100% sand. Drains instantly. 25 years later and I believe I have another 5 years to go , before replacing. They are attached by 5″ long nails, driven into the concrete wall behind the 2″ insulation.
Ontario
Ladislav
Architect
buildingadvisor says
For those who are unfamiliar, Wonderboard was one of the original cement backerboards developed as a substrate for ceramic tile. It is 1/2 in. thick and very heavy. Now there are many cement and fiber-cement boards on the market. All are durable and mostly impervious to water, but some are not suitable for ground-contact and may degrade or delaminate over time. Best to check with the manufacturer of the panel you are considering.
There are also a wide variety of products made for this application: various pargings (over fiberglass or metal lath) as well as panels made from fiberglass, vinyl, and fiber-cement. Durability is important as this area gets a lot of abuse from lawn mowers, weed wackers, baseballs, etc.
Todd says
Best To Insulate Rim Joist & Foundation on Exterior
In most states, energy codes require continuous insulation over the exterior sheathing and foundation walls below grade as a requirement. Insulating the rim joists on the interior only is terrible advice and avoids the problem. This would never pass ECC analysis.
Being a builder doesn’t mean you understand thermodynamics. Leave building technology to professional engineers and architects and stop fighting them at every turn because you don’t understand the details or “never done it before”. Instead work with them to find solutions. The industry would be better for it. This is coming from a contractor…
buildingadvisor says
There is no perfect wall system — each has pros and cons. Exterior foam insulation has the benefit of warming the wall cavity and reducing the likelihood of condensation in the wall. To a builder, it also presents a number of detailing challenges around installing and flashing windows and doors, and securing siding, and exterior trim.
Exterior foam also drastically cuts the building’s ability to dry to exterior if the wall cavity gets wet from leaky window flashing or other exterior details — probably the number one complaint in residential construction today. Combined with an interior vapor barrier and a good source of moisture, exterior foam can lead to disaster, as I once saw in a severely rotted timber frame with exterior foam.
There are many ways to create a tight, well-insulated building shell. I agree with you that insulating the band joists on the exterior is the best option, but is not always feasible. Insulating rim joists on the interior with spray foam or foam boards blocks cut and sealed in place with canned foam is another good option that has worked well in many houses.
As for foundation insulation, I prefer the interior approach for all the reasons mentioned. As for energy performance, the difference between interior and exterior basement insulation is negligible. This is well documented in the Foundation Design Handbook by ORNL and numerous other studies.
Robert H Thompson says
Thank you, Steve, for prompt and extremely helpful advice. The inspection gap sounds like a good idea.
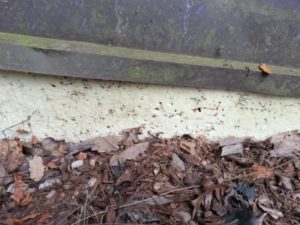
I might add that in some hillside areas of my house the grade actually comes slightly above the flashing, so presumably the foam is completely underground. The inspectors who come annually as part of our termite policy have never said a word about this, nor did the independent inspector we hired when buying the house. But it has always been in the back of my mind. Might be time to deal with it.
Thanks again!